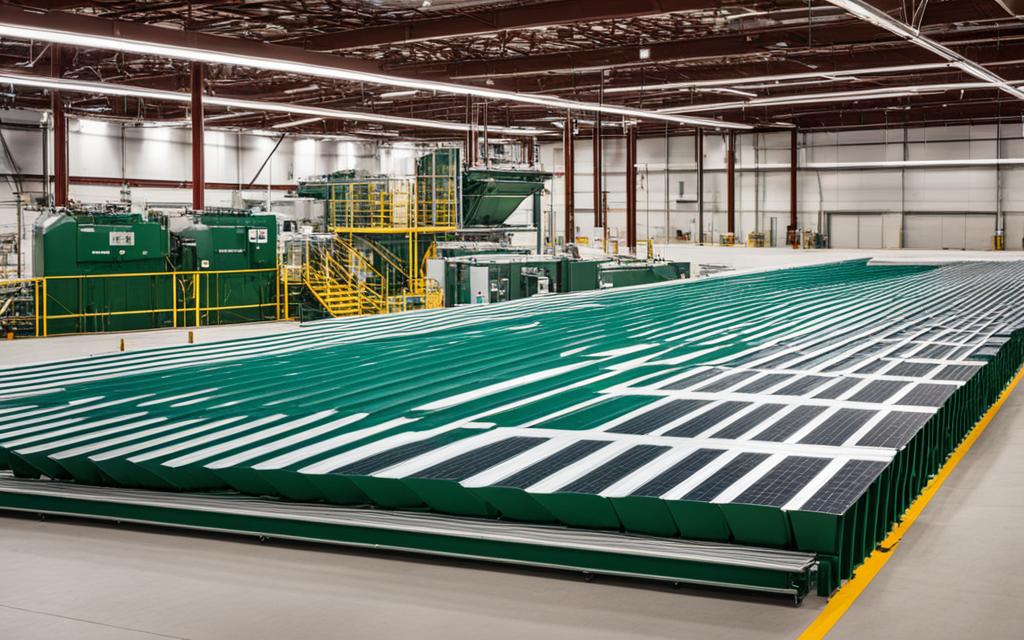
Efficiency And Sustainability In Manufacturing
The industrial pledge to advance environmental sustainability is no longer a discretionary choice, but a strategic imperative in the face of global climate challenges.
As bastions of energy consumption and greenhouse gas emissions, manufacturing companies bear a significant burden of accountability.
In a bid to meet stringent climate goals, industries are increasingly deploying sustainable manufacturing processes that maximize efficiency and usher forth a revolution in ecological stewardship.
To grasp the full landscape of change, one must consider the emergence of technologies like solvent recovery systems, which, while only a fraction of the solution, contribute meaningfully towards a larger narrative of innovation and change.
It’s the adoption of vital efficient manufacturing practices that sits at the core of the matter, serving as a blueprint for a future where economic growth navigates hand-in-hand with environmental care.
The transformation is evident as pioneering companies harness the power of renewable energy, streamline operations through lean manufacturing principles, and redefine waste into worthwhile inputs for new production cycles.
Such endeavors reduce carbon footprints and pave the way for tangible economic benefits, aligning business strategies with an ever-increasing societal demand for sustainability.
Among the exemplary figures spearheading this journey stands UBQ Materials, a company redefining the value chain by converting household waste into bio-based materials.
Such examples set a precedent, illuminating the profound impact that sustainable practices have in propelling the industry towards a more resilient and conscientious future.
Key Takeaways
- Adoption of sustainable manufacturing processes is vital for aligning with global climate goals.
- Efficient manufacturing practices significantly reduce energy usage and emissions, contributing to environmental sustainability.
- Innovative companies are transforming waste into valuable resources, exemplifying the industry’s capacity for positive change.
- Combining renewable energy with efficient practices creates a synergy of economic and environmental benefits.
- The case of UBQ Materials highlights the practical potential of sustainable inputs in modern manufacturing.
- Commitment to sustainability is both a corporate responsibility and an avenue to gain competitive advantage.
Exploring The Shift To Sustainable Manufacturing
The landscape of manufacturing is undergoing a significant transformation as businesses worldwide recognize the necessity to integrate sustainable practices into their operations.
This change is not solely driven by environmental concerns but also the prospect of achieving greater resource efficiency and cost effectiveness.
At the core of this transition is the commitment to minimize the environmental impact while embracing green manufacturing initiatives that offer a blueprint for industry innovation and economic resilience.
The Importance Of Sustainable Processes In Achieving Climate Goals
In a world where climate change poses a formidable challenge, the adoption of sustainable manufacturing processes has become critical.
These processes not only reduce greenhouse gas emissions and consumption of non-renewable resources but also align industrial practices with international climate goals.
Sustainable manufacturing champions the ethos of doing more with less—maximizing productivity while minimizing waste and energy use.
Thereby, it stands as a pillar for industries committed to environmental stewardship and the betterment of our planet.
Cost Benefits Of Implementing Sustainable Manufacturing Strategies
The fiscal advantages of sustainable manufacturing are tangibly felt across an enterprise’s balance sheet.
Enhanced resource efficiency leads to a direct reduction in raw material costs, while energy-efficient technologies decrease utility expenses.
Moreover, companies implementing sustainable strategies are often met with tax incentives, grant opportunities, and leakage-preventative benefits, safeguarding businesses from fluctuating commodity prices.
These forward-looking firms gain a competitive edge, distinguishing themselves within the market.
Transitioning From Traditional To Eco-friendly Production
As we step away from traditional production paradigms, a new era of eco-friendly manufacturing emerges.
This transition extends beyond the walls of the production facilities—it is reflected in the global supply chains and life cycles of products.
Implementing practices such as the use of biobased materials and closed-loop systems represents a holistic approach to production that conserves resources for future generations.
Moreover, advancements like recovery systems embody the meticulous efforts being made in every facet of manufacturing to protect our environment while promoting sustainable growth and development.
Challenges In Conventional Manufacturing And Environmental Impact
The industrial sector has long been associated with environmental challenges, most notably seen in conventional manufacturing practices.
Such methods have historically prioritized production efficacy without sufficient regard for the manufacturing impacts that can lead to significant resource depletion and an increased carbon footprint.
These pressing concerns are reshaping the discourse around manufacturing methodologies.
One of the core issues in traditional manufacturing is the extensive use of energy, predominantly sourced from non-renewable resources.
The dependence on such resources not only exacerbates resource depletion but also contributes to heightened environmental pollutants, including greenhouse gases.
As a result, the industrial carbon footprint has become a critical focus area for those seeking to mitigate adverse ecological effects.
The generation of substantial waste is yet another consequence of these long-standing production techniques.
The improper disposal and treatment of this waste further inflict harm on natural ecosystems, leading to pollution and the degradation of biodiversity.
In the face of these challenges, a transition to sustainable manufacturing is not just desirable but a necessity.
Driving this change necessitates a collaborative approach.
Industry associations are urging members to consider the environment in their operational processes.
Research institutions are diligently working on developing new technologies that can revolutionize energy and material usage in manufacturing.
Together, they aim to demystify consumption patterns and spearhead innovations that can substantially reduce the carbon footprint across the manufacturing landscape.
One such innovation is the investment in digital technologies, which can play a pivotal role in optimizing manufacturing processes.
By leveraging these advancements, manufacturers can improve efficiency, reduce waste, and cut down on production costs, all while minimizing their environmental impact.
Practices like these systems could be a part of the solution, redefining the dynamics of manufacturing and environmental stewardship.
It is clear that the current trajectory of conventional manufacturing is untenable. Embracing a sustainable future is not only necessary for the health of our planet but also for the economic vitality of the manufacturing industry.
- Intensive energy use and reliance on non-renewable resources lead to significant environmental ramifications.
- Significant waste generation from conventional manufacturing processes contributes to environmental degradation.
- Adopting sustainable manufacturing is essential to reducing the industrial carbon footprint and conserving resources.
- Collaboration and digital technology investment are key to optimizing manufacturing processes and mitigating environmental impacts.
Technological Innovations Driving Sustainable Manufacturing
The landscape of modern manufacturing is undergoing a significant transformation, spearheaded by digital technology in manufacturing.
These technological leaps forward align with sustainability goals, paving the way for greener and more efficient production methods.
Key among these innovations is the integration of lean manufacturing frameworks with digital capabilities, which allows for unprecedented levels of production optimization.
Lean Manufacturing And Digital Transformation
Lean manufacturing techniques have long been valued for their ability to minimize waste and enhance efficiency.
When fused with the latest digital innovations, manufacturers gain a powerful toolkit for analysis and improvement.
Real-time data analytics, for instance, can reveal energy hotspots or highlight procedural inefficiencies that, once addressed, contribute to an overall reduction in resource consumption and waste.
Integrating Renewable Energy And Automation Into Production
The manufacturing sector’s commitment to sustainability is evident through the increased adoption of renewable energy sources.
This sustainable innovation is not just an environmental decision—it’s becoming a financially savvy one.
Organizations are diversifying energy portfolios through solar, wind, and bioenergy solutions, with initiatives like power purchase agreements to facilitate this transition.
Automation further compounds these benefits by streamlining processes and reducing the energy overhead associated with production.
One often overlooked component critical to enhancing the effectiveness of manufacturing processes is the incorporation of recovery systems.
Designed to recover and reuse solvents used in production, these systems reduce the need for new solvents and limit environmental pollution, reflecting the industry’s broader commitment to environmental stewardship.
As these systems gain traction, they serve as a testament to the power of integrating economically and environmentally conscious practices within the manufacturing sector.
- Optimization of energy consumption using smart grids and IoT devices
- Machine learning algorithms for predictive maintenance, reducing downtime
- Solar and wind energy installations at manufacturing sites
- Use of biodegradable and recyclable materials in production
Together, these concerted efforts to embrace digital technology and renewable energy are not just creating greener manufacturing systems but also ensuring they remain economically competitive.
By leveraging sustainable innovations, the manufacturing industry positions itself as a leader in production optimization and a protagonist in the narrative of global sustainability.
Sustainable Materials And Resource Conservation
The quest for environmental sustainability is driving innovation across manufacturing landscapes.
Spearheading this revolution are companies like UBQ Materials, which exemplify the transformative power of sustainable materials in promoting resource conservation and reinforcing the principles of a circular economy.
By converting municipal waste into renewable bio-based materials, UBQ Materials not only champions the reduction of landfill reliance but also contributes directly to the reduction of carbon emissions.
These sustainable materials, born from the ingenuity of waste-to-material technology, exhibit a promising compatibility with a broad range of manufacturing processes.
Their adaptability makes them an invaluable asset in the quest to replace traditional, resource-intensive raw materials with more environmentally conscious alternatives.
The incorporation of UBQ’s patented material into various product lines demonstrates a commitment to not only industrial innovation but also to the meticulous stewardship of our planet’s resources.
It’s not just the versatility that sets these materials apart; it’s also their role in the creation of a more sustainable manufacturing cycle.
As industries worldwide continue to seek greener pathways, the use of materials that support a circular economy becomes increasingly crucial.
- Reduction of fossil fuel dependency
- Lower greenhouse gas emissions
- Enhanced material recyclability and versatility
- Support for the circular economy
By integrating sustainable materials into the production cycle, a tangible shift towards eco-friendly manufacturing can be actualized, leaving a positive footprint on both the environment and the economy.
Cost Analysis: The Economic Benefits Of Going Green
As the manufacturing sector evolves, a striking paradigm shift is noticeable towards practices that not only support the environment but also bring robust economic incentives.
In an era where green manufacturing benefits are increasingly recognized, this section explores the tangible financial rewards that sustainable methods yield for businesses.
Long-Term Financial Incentives For Sustainable Practices
Adopting sustainable manufacturing practices goes beyond moral and environmental responsibilities; it also makes sound economic sense.
Energy-efficient machinery, waste reduction protocols, and recycling initiatives are not just prudent for the planet—these measures can substantially reduce operational costs in the long run.
Manufacturers can achieve long-term savings through lower utility bills, minimized waste handling fees, and optimized use of raw materials.
Moreover, companies utilizing sustainable practices often see an uptick in brand loyalty among consumers, with the green credentials translating to increased market share and potential price premiums on products.
Furthermore, investors are progressively on the lookout for businesses that demonstrate a commitment to sustainability, seeing them as lower-risk and more sustainable investments.
Impact Of Governmental Incentives And Regulatory Compliance
Aligning with regulatory standards serves as another economic springboard, along with operational improvements.
Various governmental schemes offer economic incentives to businesses that are proactive about their environmental impact.
Tax credits, grants, and rebates for eco-friendly projects are just a few avenues through which companies can offset the initial costs of green upgrades.
Compliance with environmental regulations not only reduces the risk of costly penalties but can also elevate a manufacturer’s standing in the industry, often leading to preferred vendor status among partners who value sustainability.
This compliance is crucial, as failing to meet standards can lead to substantial fines and damage to a company’s reputation, undermining gains from green initiatives.
By combining improved operational efficiency with the strategic utilization of governmental incentives, manufacturers can accrue a competitive edge, ultimately leading to significant financial gains and a positive return on investment for sustainable changes.
- Lower long-term operational costs through energy efficiency and material conservation.
- Enhanced company valuation and brand perception among eco-conscious customers and investors.
- Economic advantages gained from adherence to regulatory standards and capturing government incentives.
Significantly, the array of benefits stemming from green manufacturing is not limited to the contexts discussed herein.
Integrated systems play a pivotal role in streamlining processes and preventing environmental harm, which further aligns with sustainable manufacturing principles while contributing to the monetary and ecological bottom line.
Building Brand Value And Consumer Trust Through Sustainability
In today’s market, the ethos of eco-conscious consumerism is not just a trend, but a driving force that shapes the way companies approach business.
Brands that invest in sustainable brand development are finding that their commitment to environmental integrity can lead to a stronger brand reputation and deeper consumer trust.
This alignment with the values of sustainability and responsibility resonates powerfully with customers who prioritize the planet’s health in their purchasing decisions.
The growing demographic of environmentally aware consumers is more inclined than ever before to support brands that demonstrate verifiable green credentials.
It’s increasingly clear that sustainability is not merely a box to check for corporate responsibility; it has become a critical element of brand identity that can distinguish a company from its competitors and foster lasting customer loyalty.
Consumers are actively seeking out brands that live up to the highest environmental standards and are willing to pay a premium for products that promise ecological sensitivity throughout their lifecycle.
More than just a moral imperative, the pursuit of sustainability is now intertwined with strategic brand positioning.
By transparently showcasing their commitment to green practices and policies, companies can tap into a more engaged and conscientious customer base.
In turn, this can lead to the ability to command higher price points, bolstered by the brand’s elevated stature among eco-aware shoppers.
- Brand loyalty and repeat business from eco-conscious consumers
- Heightened market presence due to positive environmental impact
- Innovative product development with sustainability at the forefront
Brands that integrate green initiatives into their core mission are not only contributing to the larger social good but are also setting the standard for what it means to be a leader in the modern marketplace.
As part of this drive toward sustainability, companies are exploring technologies that exemplify the kind of innovative processes that minimize ecological impact while maximizing efficiency.
Ultimately, the path to elevating brand value and customer loyalty is clearly paved with sustainable intentions and actions.
In an era where shoppers are discerning and value-driven, companies must adapt and embrace the ethos of eco-conscious consumerism to remain relevant and successful.
Through intentional and authentic sustainable brand development, companies not only contribute to a healthier planet but also unlock the potential for profound growth and enduring market relevance.
Cutting-Edge Case Studies: Successes In Eco-Friendly Manufacturing
In the panorama of modern manufacturing, sustainable practices serve as both a beacon of innovation and a blueprint for corporate responsibility.
A deeper look into the application of UBQ Materials across various industry heavyweights offers compelling case studies that underscore the strides made in eco-friendly manufacturing.
This exploration not only showcases the practical use of these materials but also illustrates a broader commitment to corporate sustainability and environmental CSR.
Revolutionizing Waste Management
Through the lens of UBQ Materials, we observe a tangible transformation in waste management strategies.
Multinational corporations such as Mercedes-Benz and PepsiCo have integrated this groundbreaking material into their operations, thereby converting what was once mere waste into a valuable commodity.
UBQ’s patented process exemplifies the vast potential of upcycled materials and offers a viable solution that aligns with sustainable developmental goals.
Corporate Social Responsibility In Action
Companies like McDonald’s, Rimax, and Teknor Apex have not only embraced UBQ Materials, they’ve also demonstrated a genuine resolve toward environmental stewardship.
The utilization of UBQ’s innovative conversion process not only reflects these companies’ forward-thinking approaches but also solidifies their reputations as leaders in corporate social responsibility.
Their conscious efforts in resource sourcing and waste reduction highlight the interconnection between industry practices and environmental impact, creating a compelling narrative of progress and purpose.
The initiatives undertaken by these corporations convey a crucial message: responsible manufacturing is not just a regulatory obligation—it’s also a strategic advantage that resonates with consumers and stakeholders alike.
Amidst a consumer market demanding greener practices, these companies stand as a testament to the power and efficacy of environmental CSR in the modern business landscape.
Such practices are not isolated efforts; they contribute to a larger tapestry of change where corporate sustainability is becoming synonymous with industry credibility and economic success.
One must note that extending such principles of eco-consciousness within manufacturing inevitably ties into other systems enhancement, further underpinning the multifaceted approach to environmental sustainability.
Advanced Solutions And Their Role In Manufacturing
The advent of these systems marks a transformative era in the manufacturing sector. It demonstrates how innovative recovery techniques can act as catalysts for improved operational efficiency and sustainability.
Such systems allow for the practical and effective preservation of both materials and energy, enabling industries to attain new levels of environmental stewardship.
Enhancing Efficiency With Innovative Recovery Techniques
In today’s competitive market, manufacturers continually seek methods to heighten productivity and reduce costs without compromising environmental integrity.
Innovative recovery techniques play a foundational role in addressing these demands, reclaiming solvents that would otherwise contribute to waste and inefficiency.
By adopting advanced technologies for solvent reclamation, companies gain the dual benefits of reducing production cycle times and reutilizing valuable resources.
Positive Environmental Impact Of Solvent Reclamation
Our ecological footprint is a matter of significant attention across all sectors, with manufacturing at the forefront of scrutiny.
The benefits of solvent reclamation extend far beyond simple economic incentives; they represent a tangible effort to preserve the environment.
Manufacturers that incorporate solvent reclamation strategies not only comply with rigorous environmental regulations but also contribute to a cleaner, more sustainable future by drastically lowering hazardous emissions and promoting the utilization of recovered solvents.
- Decrease in hazardous waste
- Reduction of volatile organic compound (VOC) emissions
- Conservation of raw materials
- Extended solvent lifecycle
The integration of these systems within manufacturing processes affirms a company’s commitment to the principles of a circular economy, where sustainability and economic growth work in synergy to achieve a greener future.
The path towards a sustainable manufacturing future is comprehensive and requires the harmonization of numerous components such as pioneering material use, the digital shift, vigilant energy stewardship, and adherence to stringent regulatory frameworks.
At the crux of this transition lies the dual commitment to operational efficiency and environmental stewardship, which enables businesses not just to reduce their ecological toll but also to unlock novel avenues for advancement, outpace competitors, and pave the way for ethical expansion.
Embracing these precepts signifies more than mere compliance; it heralds an era of industry transformation that echoes across global markets.
In the pursuit of sustainability, technologies like solvent recovery systems exemplify the types of strategic innovations that bolster environmental objectives while bolstering economic performance.
The implementation of such technologies is a testament to the industry’s capacity for ingenuity and its pivotal role in crafting a legacy of durability and responsibility.
It is a testament to the belief that industry and ecology need not be at odds, but can indeed flourish in concert.
As new norms and standards begin to unfurl within the sector, manufacturers are poised to lead the charge in redefining what it means to be a trailblazer in the modern industrial age.
By steadfastly pursuing a sustainable agenda, companies can contribute to a movement that transcends the bottom line, fostering a world where the health of the environment and the vibrancy of commerce are seen not as separate paths, but as one cohesive journey towards global betterment and prosperity.